By William M. Plate Jr. [Public domain], via Wikimedia Commons
How Is Nitriding Done?
Nitriding is a thermochemical process. There are several different nitriding methods including gas nitriding, salt bath nitriding, and plasma nitriding. In all of these cases, the case or outer layer of the steel is heated to 450–600 degrees Celsius while nitrogen is diffused into the substrate. This creates nitrides, or nitrogen alloys. The nitrogen itself is present at a level below six percent to guarantee the creation of g’-nitride or Fe4N, a brittle alloy that hurts part performance. At higher levels, e-nitride would form. e-nitride or Fe3N is similar and may be mixed in with the g’-nitride. The process may add other minerals to create additional, strong alloys in the steel or iron’s substrate. For example, they may be alloyed with molybdenum and chromium. This improves their suitability through quenching. Aluminum and vanadium may be included as nitriding agents. Nitriding depth ranges from 0.1 to 0.7 millimeters. Nitriding time ranges from a few hours up to a hundred hours.
How Does Nitriding Differ from Other Case-Hardening Methods?
Nitriding differs from traditional case-hardening methods like carburizing. The steel is held at the same high temperature as nitrogen is introduced. There is no transformation phase during the cooling process. In contrast, carburizing results in a phase transformation when the substrate is cooled. The carbon content of the steel absorbs carbon and the chemical composition shifts from austenite to martensite. Martensite has greater wear resistance thanks to its high hardness. Nitrocarburizing is a similar process to nitriding. The greatest difference between nitriding and nitrocarburizing is that the latter forces carbon into the surface layer of the metal. Furthermore, nitrocarburizing can only be done to ferrous alloys like steel. Note that nitride steels usually have some carbon content—typically between 0.02% and 0.45%, though carbon steels can also be nitrided. Nitrocarburizing is done for the same reasons as nitriding, such as case-hardening steel for gears or metal guides. However, nitrocarburizing is much faster than nitriding. A long nitrocarburizing process takes up to six hours. Another difference between nitrocarburizing and nitriding is that nitrocarburizing takes place at much higher temperatures, typically around 970 degrees Celsius.
What Are the Benefits of Nitriding?
One of the greatest benefits of nitriding is that it minimizes the distortions that occur during carburizing and quenching, the two most popular heat-treatment processes. This creates a much smoother surface, which in turn reduces the need for post-heat-treatment machining or finishing processes. However, nitriding does not eliminate the need for further processing. Older nitriding processes create a white layer of g’-nitride (Fe4N) that needs to be removed, though a few newer nitriding processes prevent the formation of this inferior steel alloy. Below this is the diffusion zone, or substrate, where the grain boundaries are altered by the formation of nitrides. Below this remains the unchanged core material. These boundaries are obvious when studied under a microscope. The hardened material has a reduced risk of galling. It has a greater resistance to tempering, and it remains strong when exposed to high temperatures. That’s one reason why nitrided steel is used in firearms, extruding dies, die-casting tools, plastic mold tools, and forging dies. Nitriding increases the fatigue strength of the metal, or the stress the material can withstand without breaking. This dramatically increases the life expectancy of tools. Nitrided metal has better dimensional stability than other heat-treated materials. Nitrided material has a lower fatigue notch sensitivity as well. Nitriding can be done to hollowed-out metal pieces. This gives the hollowed-out area of a part better mechanical support. It also reduces the risk of cracking caused by elastic deformation, while nitrided parts are also less likely to deform in the first place.
When Isn’t Nitriding the Best Option?
While nitriding creates high surface hardness, it isn’t always going to be the best choice. For example, abrasive-wear applications can still wear down 1nitride steel. High point loads may chip away the nitrided layer. However, nitrided steel is a good choice for adhesive-wear applications. This is because the nitrided surface reduces friction while maintaining its corrosion resistance. This article is accurate and true to the best of the author’s knowledge. Content is for informational or entertainment purposes only and does not substitute for personal counsel or professional advice in business, financial, legal, or technical matters. © 2020 Tamara Wilhite
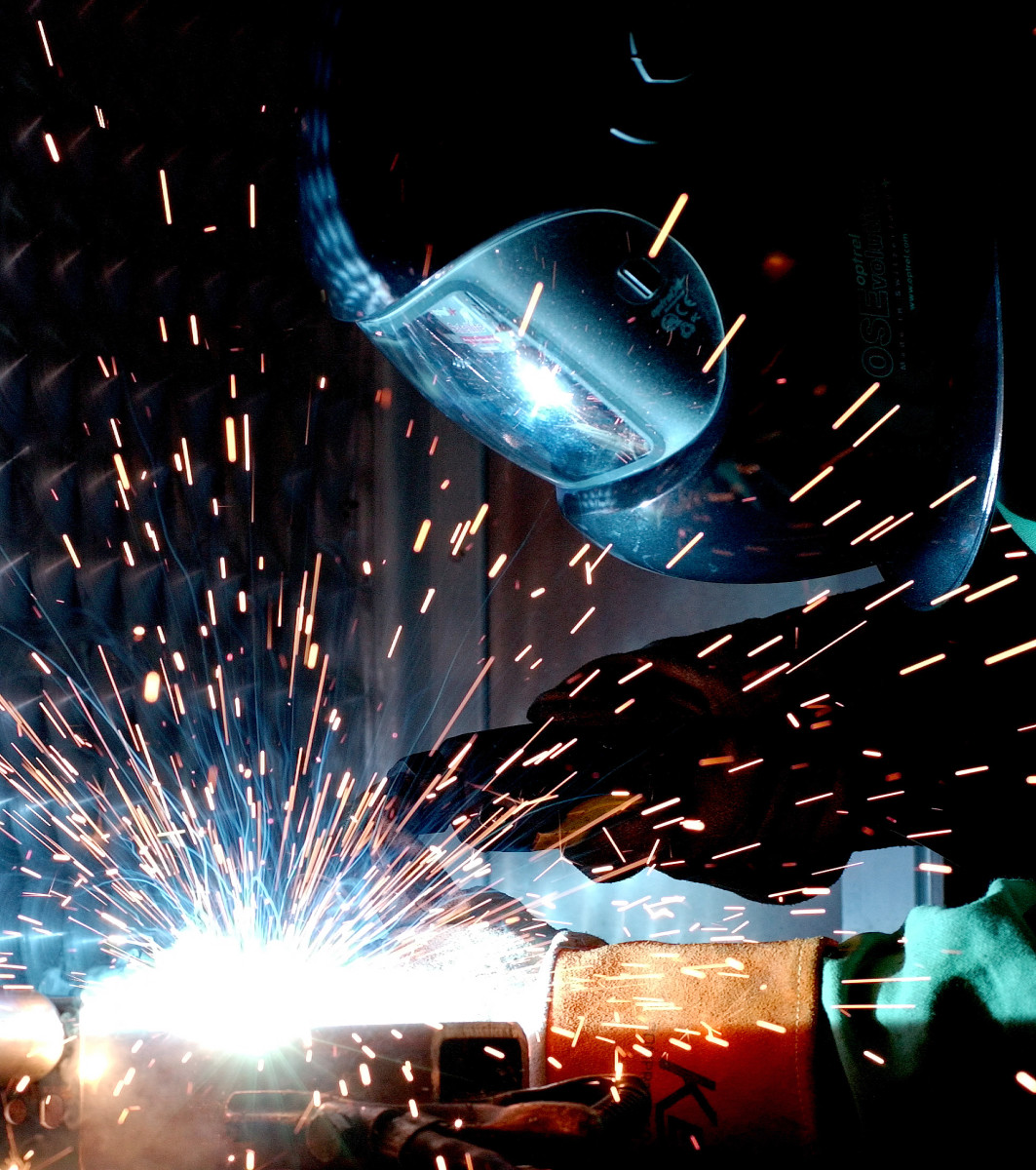